Cline's Comments |
|
New Method Lowers PUR System Costs |
|
The use of PUR for bookbinding in the U.S. has increased steadily since the first trials were run in 1988. Initially, users had three main concerns. First, the product needed 24 hours to cure before packing and shipping. Second were concerns about one of the components of the PUR, namely MDI (methylene bisphenol di-isocyanate). Third, the initial cost of the equipment as well as the maintenance can be very high. |
|
The first concern has been addressed by the development of newer PURs that now provide books that can be handled within minutes and trimmed within 30 seconds of binding. These books continue to develop strength, but can be shipped immediately while the moisture in the paper finishes the curing process. The second concern, MDI, has been monitored carefully at various locations. The fact that MDI combines rapidly with moisture in the air as well as being heavier than air shows this concern to be minimal |
|
Independent studies have reported no cases where the emission levels have exceeded those permitted by OSHA. |
|
The third concern, equipment cost, I would like to address in this article. The early PUR equipment required a separate applicator pot, controller panel, and PUR unloading system. These systems are not without maintenance problems, including resurfacing the rollers, recalibrating the thermal systems, and monitoring the adhesive level in the pot. Some of the binder manufacturers have realized the need for more compatible systems and are offering PUR pots as options for the original machines. |
|
New Method |
|
For those customers who now want to retrofit their existing binder to use PUR, there is another alternative. This method uses a closed system to extrude the PUR onto the cover as it is being fed to the cover attachment station. Extrusion has been investigated in the past for hot melts as well as PUR. Past tests with PUR were conducted by extruding the PUR upwards onto the backbone of the book. These tests were generally unsuccessful due to the variation in clamp height and the need to apply a very thin layer of PUR. The head would either hit the book or miss the book completely. |
|
The new method applies the PUR downward onto the cover and can be controlled precisely. With easy-to-bond paper, such as ground wood or uncoated offset paper, the PUR alone is satisfactory. However, when coated paper is used, a patented system called TWINFLEX 2000 is needed. |
|
Primer System |
|
The TWINFLEX 2000 system includes a liquid pre-primer and a liquid primer applied to the backbone of the book and dried before putting on the cover. Both the primer and the pre-primer are applied in very low levels, leaving some of the fibers protruding through the film. |
|
The purpose of the pre-primer is to wet out the surface of the milled backbone and to penetrate into the fibers easily. This pre-primer is generally very low viscosity and actually "splits" the ends of the fibers. Once they are split, the primer will penetrate further into the spine and provide excellent anchorage to the paper. This process is especially helpful with cross grain paper because the ends of the fibers are perpendicular to the spine. |
|
The primer is a typical emulsion product. It is low viscosity, which allows it to be absorbed into the paper fibers more easily. Because the film coating is very light, it can be dried very easily, and the machine can run at high speeds with minimal heat applied. |
|
The PUR application system is a closed system which prevents the escape of MDI. The application head mounts directly after the scoring wheels on the cover feeder. This allows the cover to be held steady while the PUR is being applied. The width of the slot extrusion nozzle is variable and therefore lays down both the backbone and the hinge glue. This makes the entire system recyclable. |
|
The initial cost of this approach is considerably less than earlier systems, and maintenance costs should also be lower. While this system may not be the answer for all binders, it will certainly fill the need of those who want to offer all the benefits of PUR bound books. |
|
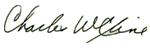 Chuck Cline |
Technical Service Manager - Bookbinding |
|